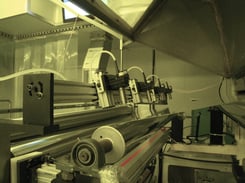
A customer presented Lumetrics with a 5 layer product constructed of a liner, adhesive, middle layer, adhesive and a liner. The product is made in two operations. The first operation coats the liner with adhesive then adds the middle layer. The second operation adds adhesive to the middle layer and then adds the final liner.
The ability to control the adhesive layer was a critical parameter. The customer needed to know the adhesive thickness when applied in a wet state and again when cured in a dry state.
Due to the adhesive, a non-contact measurement system was required. The Lumetrics OptiGauge was the perfect solution. Lumetrics installed an OptiGauge with an 8-Port Optical Switch, custom control software and, 8 probes mounted at 3 locations .
The probes are located in the Adhesive Wet stage, Adhesive Dry stage and in the Final stage. During the first operation the thickness of the adhesive and liner are measured by the first two probe locations. The liner, adhesive and middle layer are measured at the final probe location. During the second operation the liner, adhesive, middle layer and adhesive are measured at the first two probe locations. The full 5 layer product is measured at the final location.
All measurements are taken while the system is running at full operating speed. The product moves under the probes allowing us to scan the entire length of the product. The feedback from the OptiGauge allows the operators to quickly make adjustments and keep all parameters within specified tolerances. This system has resulted in the customer being able operate with greater efficiency both in terms of production and cost.
COMMENTS